The application of sandstone in the field of architecture is quite prevalent due to its hard-wearing characteristics. In addition, the precise level of finishing in sandstone makes it an ideal choice for a wide range of applications like paving, flooring, wall cladding, etc. In the field of natural stone, calibration is one of the most commonly used terms. What does calibration mean? What is calibrated sandstone? Since India is a leading supplier of sandstone, we will also get to know the meaning of Indian calibrated sandstone.
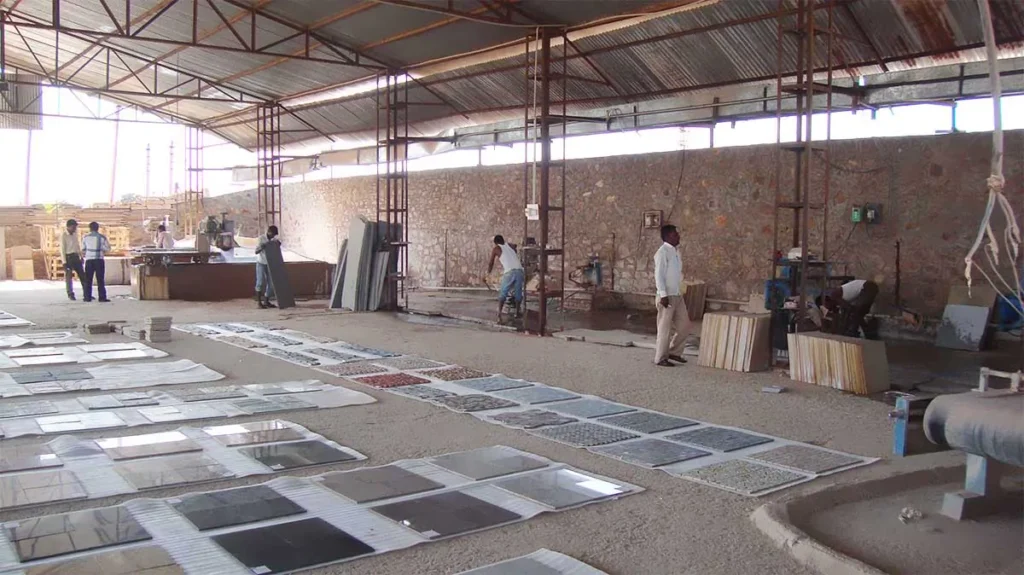
What does calibration mean?
Typically, calibration major refers to the process of regulating the output or sign on a measurement apparatus to abide by the value of the chosen standard, within a particular precision. It can also be defined as a combination of two processes: calibration and adjustment.
What is calibrated sandstone?
The calibration refers to a mechanical process sandstone undergoes to maintain uniform depth. This further paves the way for its easier and smoother installation. The bottom line is that Indian sandstone is a completely natural substance. It makes sense that very few natural materials adhere to a perfectly homogeneous build and structure; in the case of Indian sandstone, this implies that there may be notable differences across stones.
This doesn’t necessarily indicate a problem; rather, it just indicates that in order to properly arrange them and obtain a flat surface, these variances must be taken into consideration. In order to ensure that the entire surface is level, the installer of uncalibrated paving must accurately determine the bed depth for each individual stone. Indian stone must be installed with a full bed of mortar.
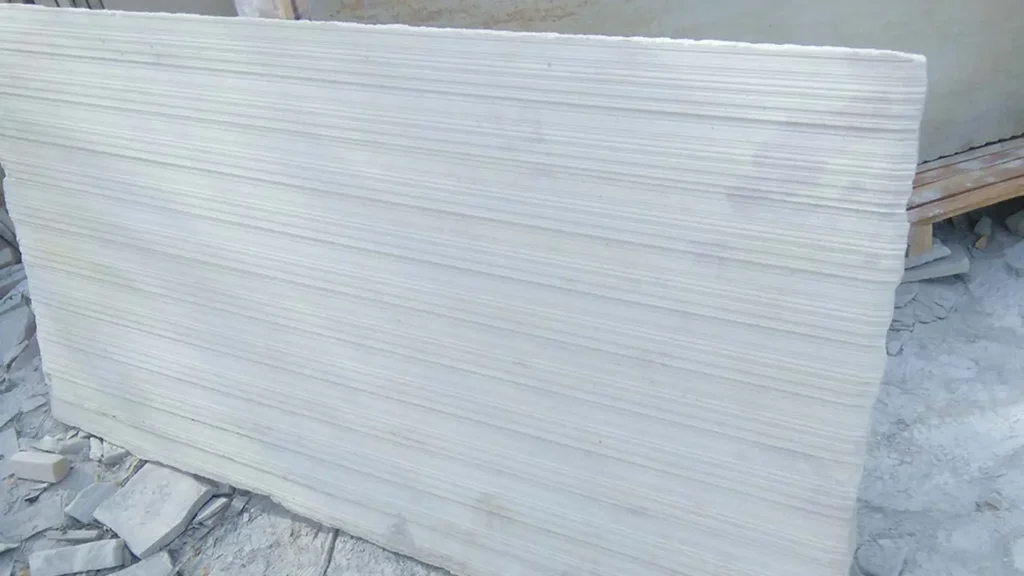
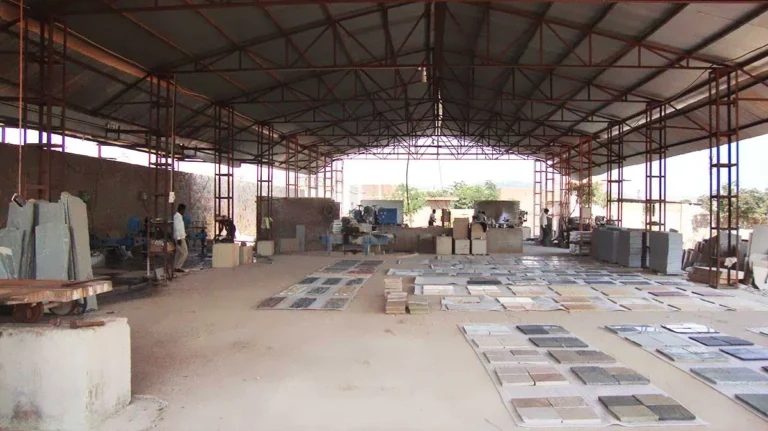
How the stone calibration is done?
Often called strip milling, the calibration process involves the passing of sandstone slabs through a string of uniformly placed saw blades. These blades are diamond edged that gives them the required strength for cutting through the stone. This process tends to produce a lot of dust and noise, thus, requiring the workers to make the use of specialized protective gear to prevent damage to their throat, lungs, or ears.
These blades cut channels or grooves into the bottom, resulting in a string or ridges extending up the length of each sandstone slab to award it a ‘toothed’ look. These teeth are further chiseled off to release a calibrated flag in the form of uniform thickness.
Benefits of Calibrated Indian Sandstone Slabs
There are numerous benefits associated with the use of calibrated Indian sandstone slabs:
For Landscapers
When slabs are calibrated, it takes less time and effort for a professional landscaper to lay them. Since paving should be done on an even surface with no protruding edge, a professional needs to leave space for slabs of varying thicknesses in the mortar layer. This asks for high levels of skills, experience, and attention to detail.
In the case of calibrated slabs, the thickness of their remains uniform. This makes it easier for landscapers to do the job as they don’t need to make adjustments to accommodate thinner or thicker slabs.
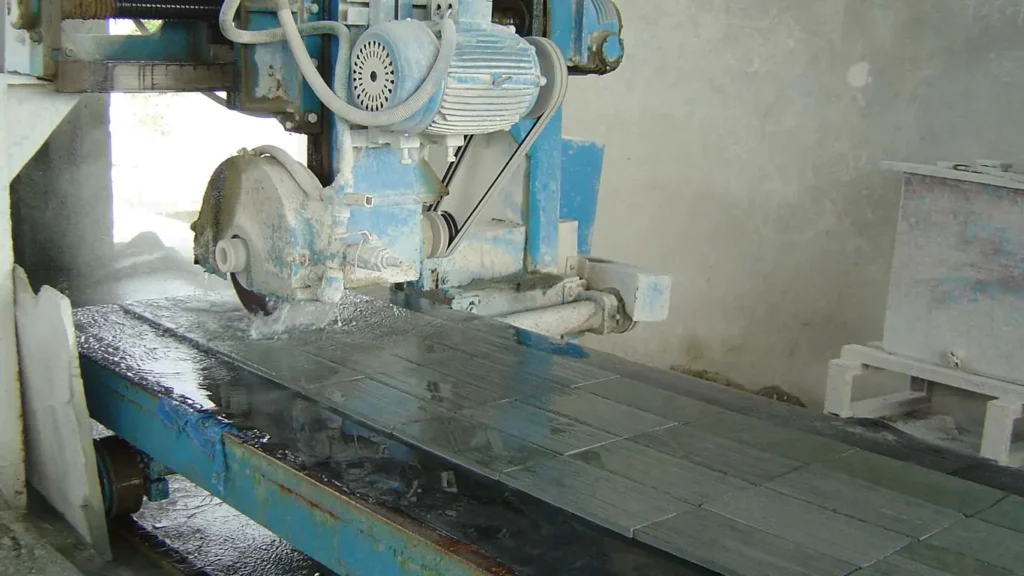
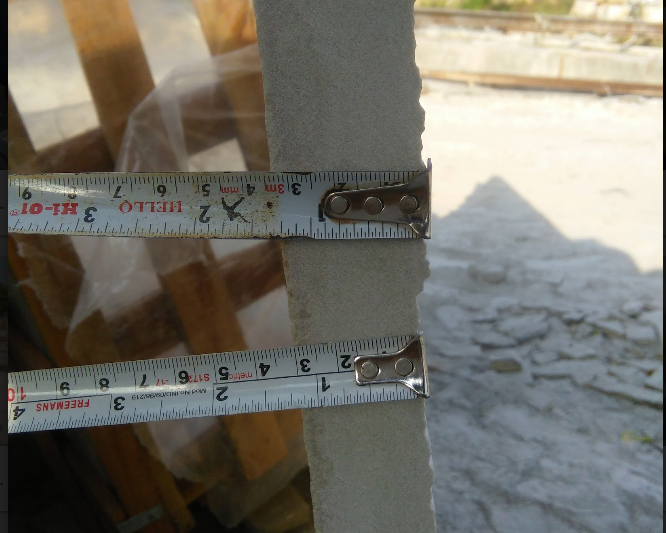
FOR SUPPLIERS AND MANUFACTURERS
Calibrated paving slabs help save costs on shipping. If the sandstone’s thickness ranges from 25 to 40mm, an average quantity of 400m2 can be put into a shipping container. However, with paving slabs calibrated to 22mm, sandstone suppliers can easily put 550m2 of quantity in one shipping container. This additional volume greatly brings down the shipping costs for importers and sets the ground for a cheaper price proposition for the customer.
The stone industry’s mechanization is a major contributing factor to the change to calibration. One procedure that needs to be completed by a machine is calibration. This de-skills the task and also makes it possible for a more consistent outcome. De-skilling helps lower labor expenses and increase employment options for a greater number of individuals.
FOR HOUSEHOLDS
Since calibrated sandstone slabs are quicker and easier to lay apart from being reasonable to transport, the ultimate benefit if passed on to the customers in terms of lower costs.
How thick is calibrated paving?
In most cases, sandstone slabs are calibrated to an extent of 22mm thickness. This is because this thickness is found to be ideal for a majority of construction applications.
Is it strong enough for my application?
It is well acknowledged that the sub-foundation beneath the paving material plays a more significant role in determining a driveway or patio’s strength than the material itself. Therefore, when paving is not adequately supported by the sub base, it will not withstand heavy traffic. It must be placed on a full mortar bed as well.
The stone’s density is a second factor to take into account. Raj Green and Kandla Grey Sandstone are two examples of sandstones that are exceptionally hard. Some are softer, like Fossil Mint, which we don’t carry.
Most paving is strong enough to endure the pressures placed on patios and pathways at 22mm. This also applies to the majority of driveways. However, it’s important to remember that paving that is 25 mm thick is surprisingly 40% stronger than that of 22 mm. Therefore, a thicker stone—especially one made of a softer material—might be wise if you live in a place where there is a lot of traffic from vehicles.
What does cutting tolerance mean?
This refers to the permissible variation in stone thickness. Being a natural material, it is nearly impossible to achieve uniform thickness in every slab. However, tolerance may also be affected by the production method.
Calibration is a hard process to perform, particularly on hard stones. A majority of sandstone manufacturers and exporters use large calibrating wheels that tends to precisely calibrate material down to permissible tolerances, of +/- 2mm.