Natural stones are popular in all parts of the world. Be it marble, sandstone or limestone, natural stones are in a huge demand.
With the increasing reach of globalization, lots of stone manufacturers, suppliers, and exporters have jumped into the competitive fray of the natural stone industry. When it comes to availing natural stone, the role of a natural stone processing factory and manufacturers becomes quite vital. Stone factories not only cut big blocks into smaller slabs and tiles but also produce quality-oriented products and articles with zero-defect assurance.
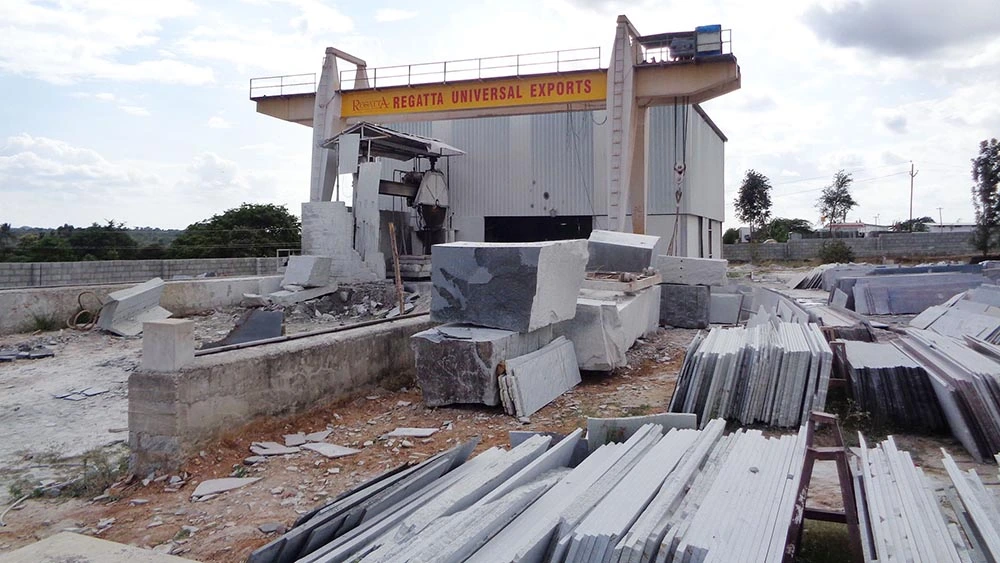
When big rough blocks are brought to natural stone factories, they are not fit to use for the decoration and construction works. At the primary stage, natural stones come with some visible defects. After passing through the processes of cutting, cleaning, wetting, drying and polishing, you get a stone product that is fit to use. Defect elimination means the natural stone product you are using is free from imperfections and errors. Regatta Universal Exports is such a name in the industry that serves its clients with high-quality natural stone processed at its fully-functional factory.
Zero-defect means mistakes are not acceptable
At a marble or sandstone quarry, the process of blasting divides rocks into bigger blocks. Then, blocks are sent to factories. There, stone cutting instruments and machines are used for the cutting purpose.
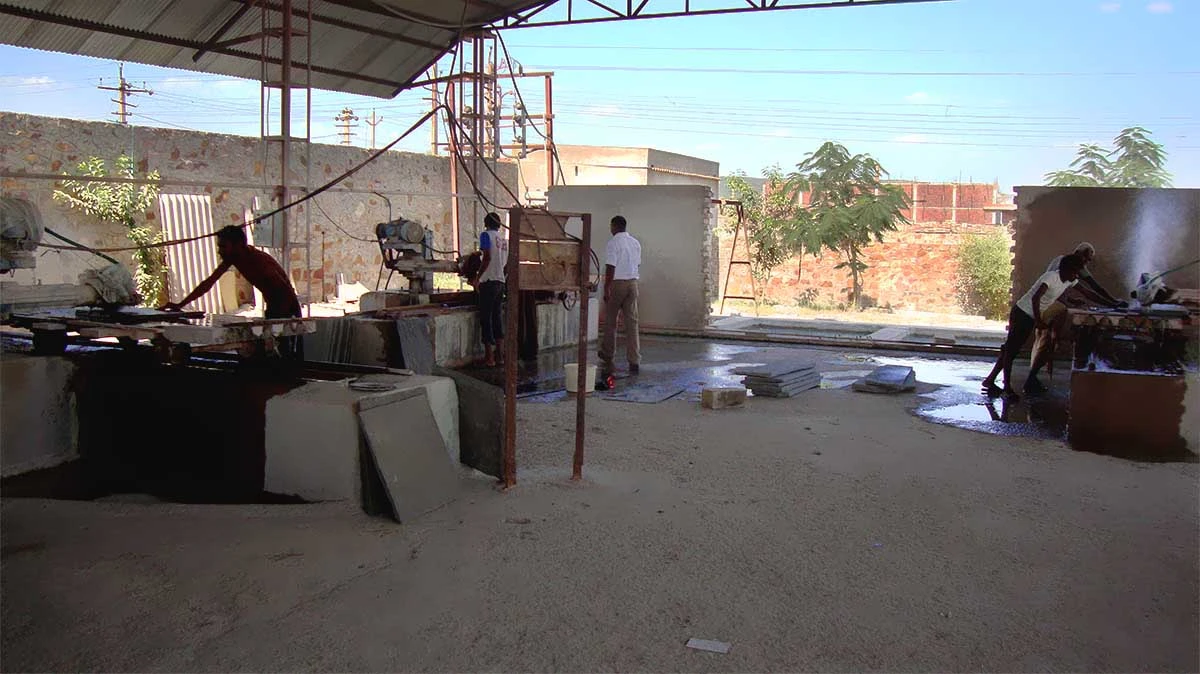
Keeping the needs and requirements of buyers in mind, stones are cut into different shapes. Then, they are cleaned with water and dried with care. After this, the process of polishing and chamfering take things to the next level. For ensuring zero-defect products at Regatta factory, following tasks are done:
- Cutting of natural stone: Gangsaw, cutter slabs, and tiles
- Polishing: Polished, honed, sandblasted, antique (sandblasted + brushed), bush hammered, bush hammered + brushed, leather finish, tumbled, and lepatora
- Ornamenting: Hand cut and machine cut edges
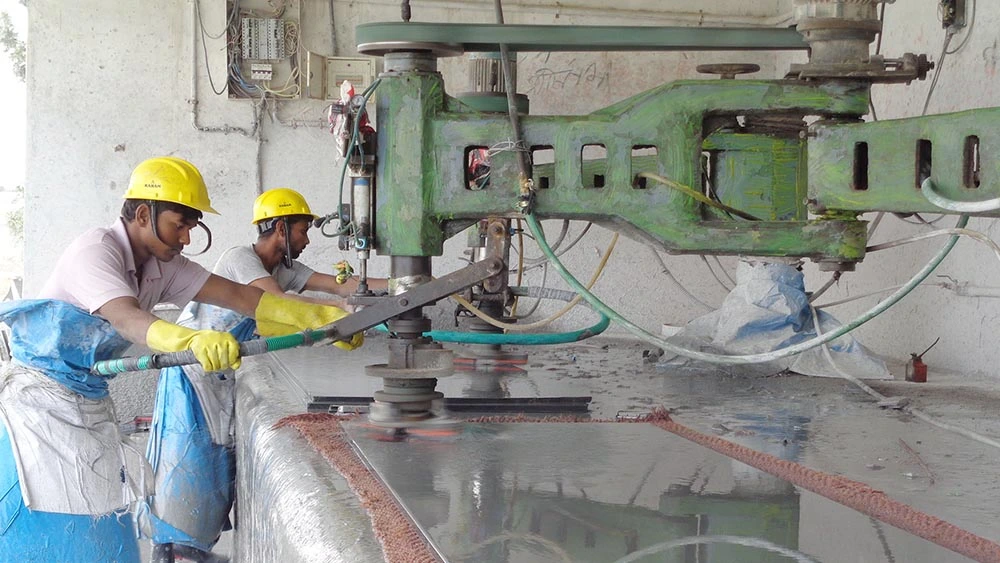
At operational natural stone factories, zero-defect is not all about making strong and functional products. It is also concerned with saving valuable time and money of buyers and end-users. That is why time management and cost control matter the most. As mistakes are not acceptable at the functional natural stone factory in India, following aspects are considered for better, effective and error-free output:
Manufacturing of natural stones as per specific needs
Fully-functional manufacturing unit
Usage of cutting-edge technology
Strict quality control at all stages
Use of the latest equipment & machinery
Adoption of global eco-friendly production practices
Well-trained and professional staff of experts
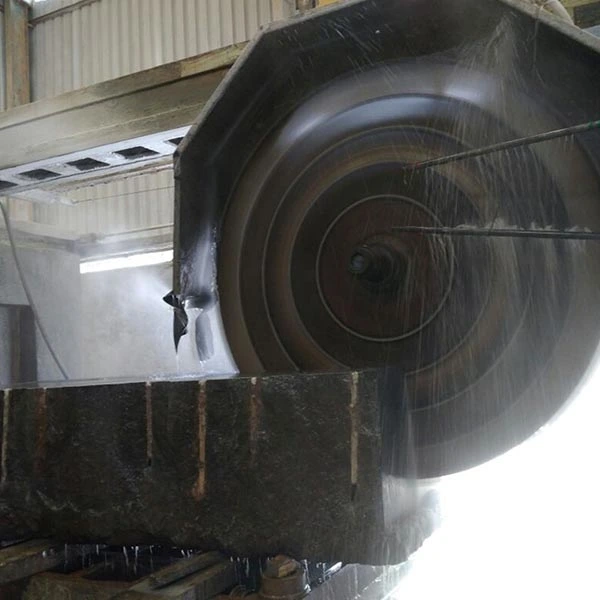
Steps involved in defect elimination processs
In a state-of-the-art manufacturing unit, there are different processes that are not restricted to cutting and polishing of the stone. They are also concerned with quality control, product packing and product delivery on time. At every stage, it is vital to eliminate defects and errors. An error-free product means it is fit to use and will match expectations of the end-users. This is how Regatta’s production team ensures defect elimination in a variety of slabs and tiles, using a proven process. This process includes:
A proactive approach to curb flaws in advance
Deployment of the quality improvement team
Regular progress monitoring under expert supervision
Strict time management for regular production
Stone size, thickness, and design monitoring
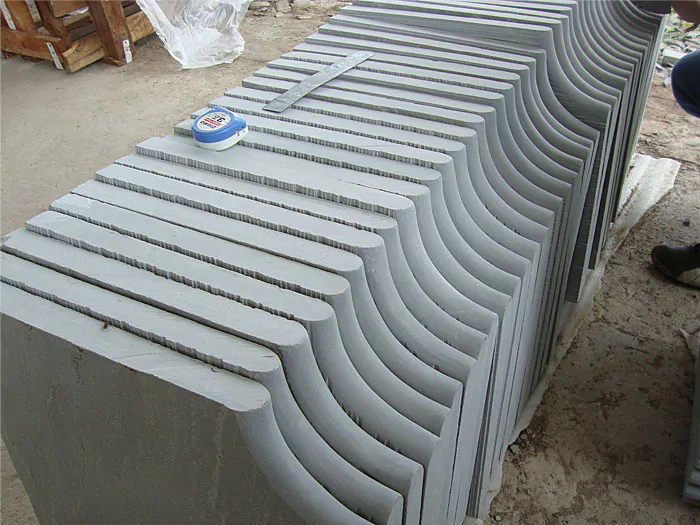
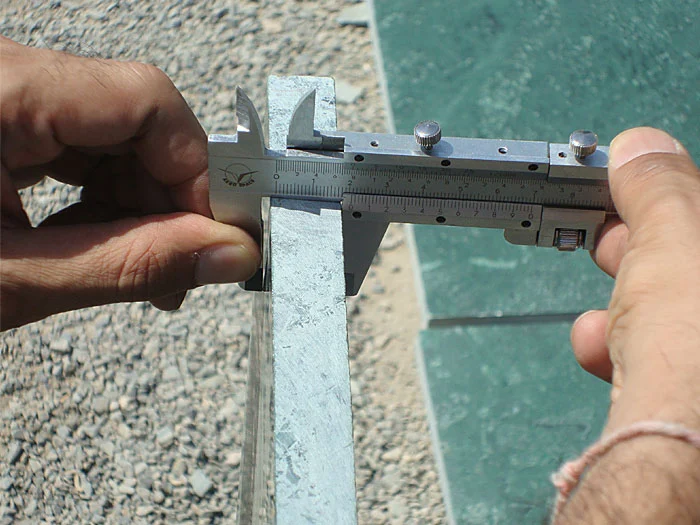
Whether you are searching for camel dust sandstone factory in India or Kota blue limestone factory in India that offer quality products, Regatta Universal Exports makes a big difference. For product information or sales inquiry, simply fill the form at contact us page.
No matter what sort of queries you have, we welcome you to our website.